Lifting Equipment Regulations: Ensuring Safety in Your Business
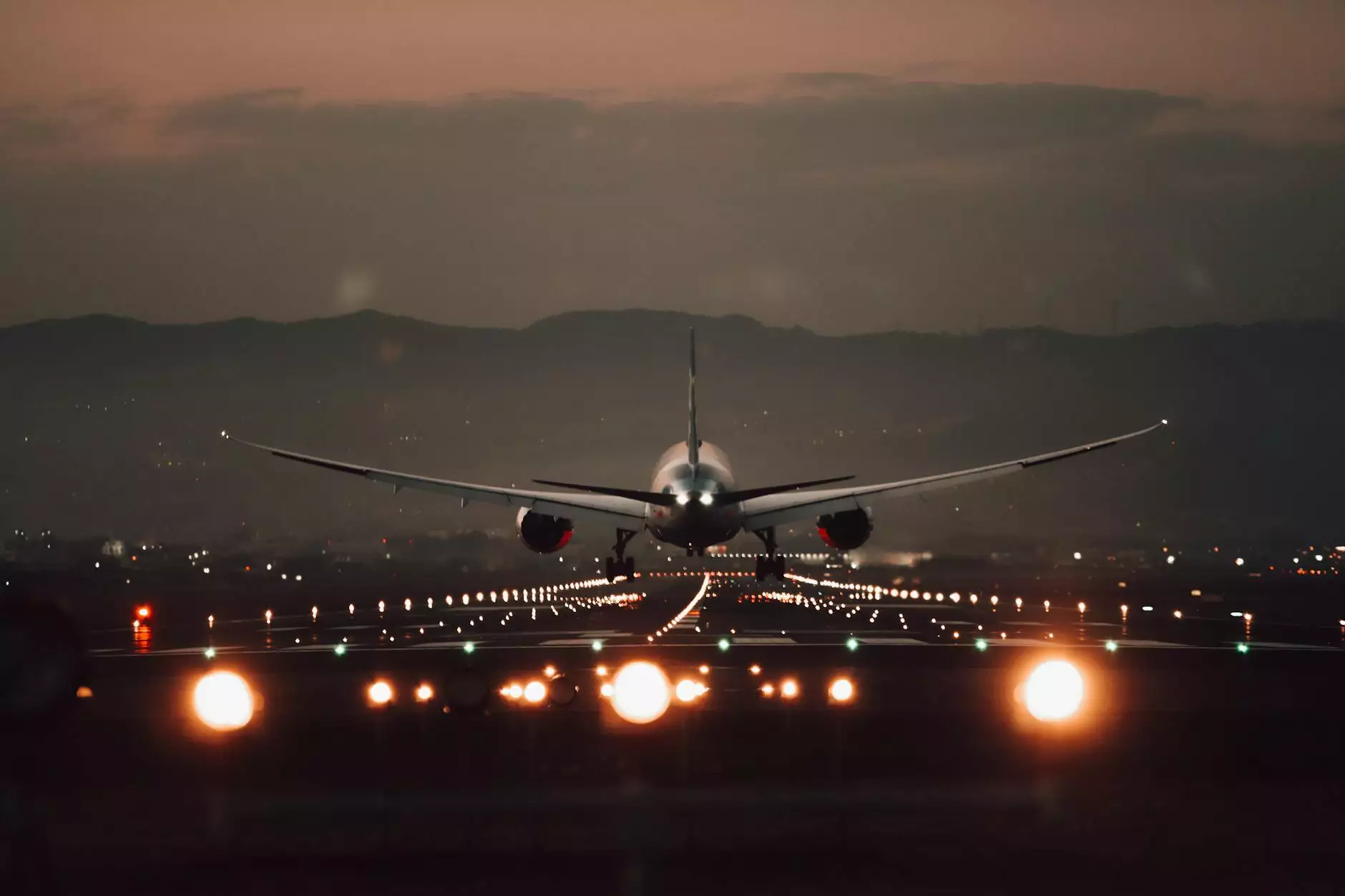
In today's fast-paced business environment, ensuring the compliance with lifting equipment regulations is paramount for maintaining operational efficiency and safety. Whether you're in the Home & Garden sector or involved in Pest Control, understanding the standards that govern lifting equipment can significantly impact your business's success and reputation.
Understanding Lifting Equipment Regulations
Lifting equipment refers to any device that is used for lifting or lowering loads. This includes cranes, hoists, elevators, and even mobile lifting devices. Each of these tools must adhere to specific regulations designed to ensure safe operation practices. Regulatory bodies outline these regulations to prevent accidents and protect workers' safety.
The Importance of Compliance
Businesses that utilize lifting equipment must comply with established regulations to minimize the risk of workplace accidents. Non-compliance can lead to serious legal repercussions, including hefty fines and shutdowns. Moreover, adherence to these regulations instills confidence among your employees and clients, establishing your brand as a responsible player in your industry.
Key Regulations Governing Lifting Equipment
Various regulations govern lifting equipment, and they can differ depending on the region and the specific type of equipment used. Below are some critical regulations that businesses should be aware of:
1. The Lifting Operations and Lifting Equipment Regulations (LOLER) 1998
In the UK, LOLER is a fundamental regulation that requires all lifting operations to be properly planned, supervised, and carried out safely. The regulation emphasizes the following:
- Thorough Examination: Lifting equipment must be thoroughly examined by a competent person at prescribed intervals.
- Usage and Maintenance: Equipment should be used according to instructions, and regular maintenance must be conducted.
- Safe Working Load (SWL): Every lifting device must have a defined SWL, which must not be exceeded.
2. The Health and Safety at Work Act 1974
This act places a legal obligation on employers to ensure the safety of workers. Under this act, employers must assess risks and implement measures to mitigate them, particularly when using lifting equipment.
3. The Provision and Use of Work Equipment Regulations (PUWER) 1998
PUWER complements LOLER by stating that all equipment used at work must be suitable for the intended use, safe to operate, and maintained in a safe condition. This regulation applies to all work equipment, including lifting devices, emphasizing the importance of:
- Training: Employees must be adequately trained to operate lifting equipment.
- Marking: Equipment should be appropriately marked with instructions for safe use and maintenance.
Best Practices for Ensuring Compliance
To ensure strict adherence to lifting equipment regulations, businesses should implement best practices. Here are some actionable strategies:
1. Conduct Regular Training and Refreshers
Training is essential in ensuring that all employees are competent in the operation of lifting equipment. Regular refresher courses will help to maintain high levels of safety awareness.
2. Maintain an Audit Trail
Regular audits of lifting equipment not only ensure compliance but also help identify potential issues before they escalate into significant problems. Keep detailed records of all inspections, repairs, and maintenance performed on the equipment.
3. Implement a Safety Management System
Integrating a comprehensive safety management system can streamline compliance efforts. This system should include:
- Risk Assessments: Regularly assess the risks associated with lifting operations.
- Incident Tracking: Document and analyze any incidents to prevent future occurrences.
- Maintenance Schedules: Create and adhere to a proactive maintenance schedule for all lifting equipment.
Common Misconceptions About Lifting Equipment Regulations
As businesses navigate through lifting equipment regulations, several misconceptions may arise:
Misconception 1: Compliance is a One-Time Event
Many businesses believe that once they meet compliance standards, they can forget about it. In reality, compliance is an ongoing process that requires continuous evaluation and adaptation to new standards.
Misconception 2: Regulations are Only for Large Businesses
Whether small or large, all businesses that utilize lifting equipment must comply with safety regulations. Small businesses often overlook this responsibility, but they are equally liable for maintaining a safe work environment.
Conclusion: Elevating Safety Standards Through Compliance
In conclusion, adhering to lifting equipment regulations is not merely a bureaucratic requirement but a vital component of a successful and safe business operation. By understanding the regulations that govern lifting equipment and implementing best practices, businesses across various sectors including Home & Garden, Gardeners, and Pest Control can enhance their safety standards and operational efficiency.
As you navigate the complexities of compliance, remember that investing in safety pays dividends in employee morale, operational efficiency, and customer trust. By prioritizing lifting equipment regulations, your business will not only meet legal requirements but also foster a strong culture of safety and compliance that resonates with clients and stakeholders alike.