Understanding the Role of Plastic Injection Mold Makers
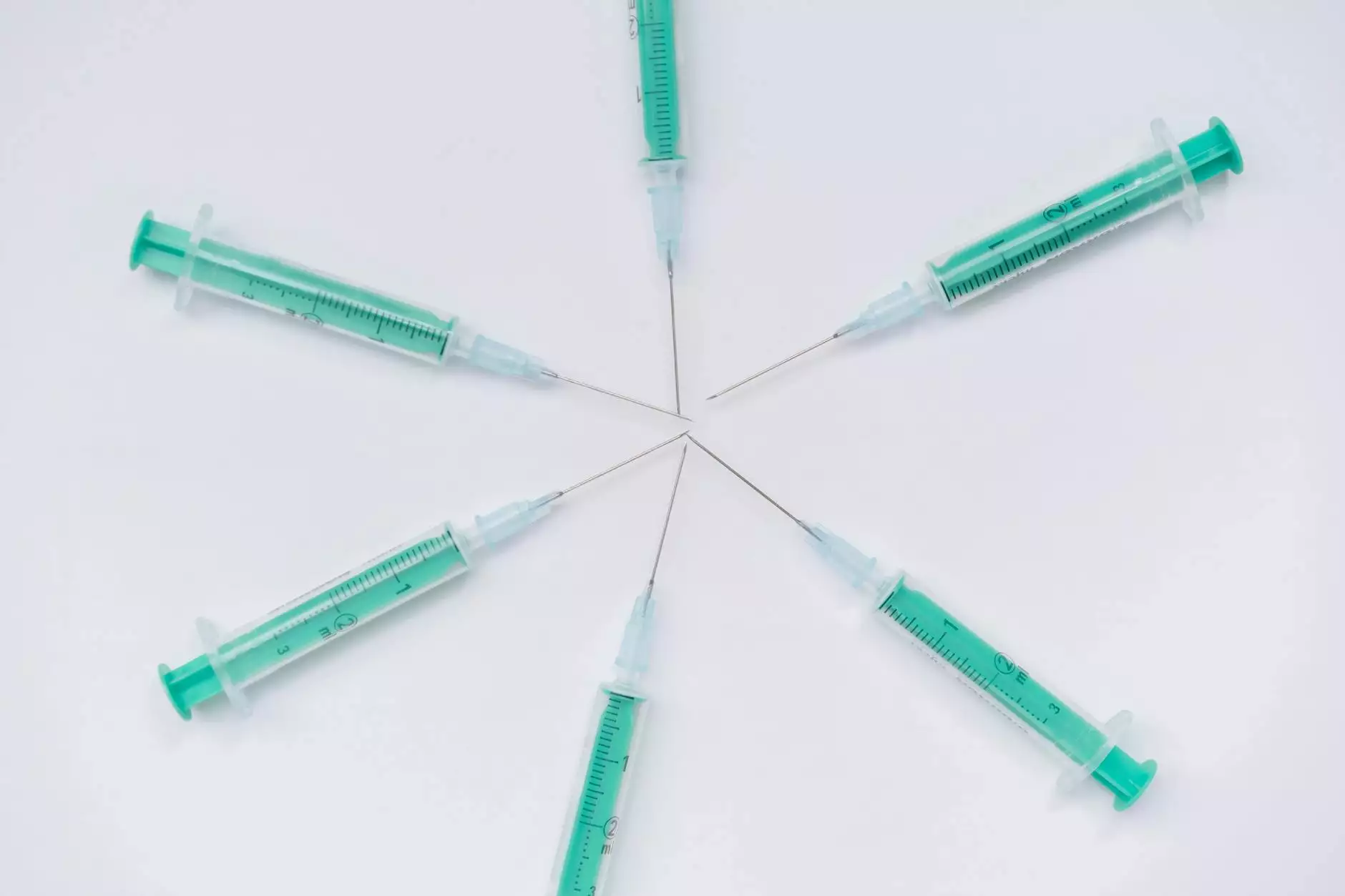
In an age where manufacturing is at the forefront of innovation, the role of plastic injection mold makers has become increasingly significant. These professionals are the backbone of the manufacturing industry, providing the raw materials and components that are crucial for the production of a myriad of products. From automotive parts to consumer goods, the expertise of plastic injection mold makers ensures not only efficiency but also meets the ever-evolving demands of the market.
What Are Plastic Injection Molds?
Before delving into the specifics of plastic injection mold makers, it's essential to understand what plastic injection molds are. Essentially, they are tools used to produce plastic parts through a process called injection molding. This process involves:
- Heating plastic materials until they melt.
- Injecting the melted plastic into a mold, which is a hollowed-out block made of metal.
- Allowing the plastic to cool and solidify, forming the desired shape.
- Removing the solidified part from the mold once it has cooled.
The Importance of Plastic Injection Mold Makers
Plastic injection mold makers play a crucial role in ensuring that the molds are created to the precise specifications required for high-quality production. Their expertise in designing and manufacturing molds allows for:
- Customization: Each mold can be tailored to specific needs, allowing businesses to create unique products.
- Efficiency: High-quality molds lead to faster production times and reduced material waste.
- Durability: Well-made molds can endure significant wear and tear, thus minimizing replacement costs.
Key Qualities of a Top Plastic Injection Mold Maker
When selecting a plastic injection mold maker, consider the following qualities that are indicative of a top-tier professional:
- Experience: An experienced mold maker brings a wealth of knowledge regarding the intricacies of the molding process.
- Technical skills: Proficiency in CAD software and machining tools is essential for accurate mold design.
- Attention to detail: Precision is paramount; any small error can result in significant waste and production delays.
- Excellent communication: A good mold maker collaborates closely with clients to understand their needs and specifications.
Steps Involved in the Injection Molding Process
The injection molding process involves several steps, each crucial for ensuring the final product meets quality standards. Here’s a breakdown:
1. Mold Design
The first step is designing the mold. This requires a thorough understanding of the product's specifications. The design phase often involves:
- Creating 3D models using CAD software.
- Considering aspects such as cooling channels and ejection systems.
- Finalizing the material to be used for the mold itself.
2. Prototype Creation
Before moving to full-scale production, a prototype may be produced. This allows for:
- Testing the mold’s efficacy.
- Identifying any design faults before large-scale manufacturing.
3. Mold Fabrication
Once the prototype is approved, the actual mold is fabricated. This involves:
- Machining the mold from solid metal blocks.
- Using CNC machines to achieve precise dimensions.
- Assembling components like inserts and cooling systems.
4. Injection Molding
After the mold is fabricated, the plastic injection process begins. This includes:
- Melting the plastic granules.
- Injecting the molten plastic into the mold under high pressure.
- Cooling the plastic to form a solid part.
5. Finishing and Quality Control
Finally, once the molded parts have cooled and solidified, they undergo finishing and quality control checks. This guarantees:
- Parts meet specified tolerances.
- Surface finishes are as requested.
- Any defects are identified and rectified.
Benefits of Working with Skilled Plastic Injection Mold Makers
Enlisting skilled plastic injection mold makers offers several benefits, including:
- Improved Product Quality: Higher quality molds lead to better, more consistent parts.
- Cost Efficiency: A skilled mold maker minimizes waste and maximizes production efficiency.
- Shorter Lead Times: Experienced makers can produce molds quicker without sacrificing quality.
- Advanced Technology: Many top mold makers leverage the latest technologies for optimal results.
Future Trends in Plastic Injection Molding
The plastic injection molding industry is continuously evolving. Here are some future trends to watch:
- Sustainability: Increasing demand for biodegradable and recyclable materials in the production process.
- Automation: The rise of automated systems in mold making and production to enhance efficiency.
- 3D Printing: Using 3D printing technology to create molds, which can reduce time and costs significantly.
- Smart Manufacturing: Integration of IoT (Internet of Things) to monitor the molding process in real time.
Choosing the Right Plastic Injection Mold Maker: A Checklist
When selecting a plastic injection mold maker, it’s crucial to evaluate potential partners based on certain criteria. Use the following checklist:
- Portfolio: Review their past projects to assess quality.
- References: Ask for testimonials from previous clients.
- Capabilities: Ensure they can handle your specific needs and volumes.
- Communication: Test their responsiveness and willingness to collaborate.
- Support Services: Check if they offer post-production support and maintenance services.
Conclusion
In conclusion, plastic injection mold makers are vital players in the manufacturing sector, ensuring products are made with precision and efficiency. Their ability to design, fabricate, and maintain molds determines the quality and cost-effectiveness of the final products. As technologies and demands evolve, so too will the role of mold makers, making it essential for businesses to stay informed of industry trends and select competent partners like Hanking Mould to navigate the complexities of plastic injection molding.
Investing in quality mold making not only improves production outcomes but also fosters innovation within product development. The future of manufacturing is bright, thanks in large part to the invaluable contributions of skilled plastic injection mold makers.