The Role of Precision Mould Making Manufacturers in Modern Industry
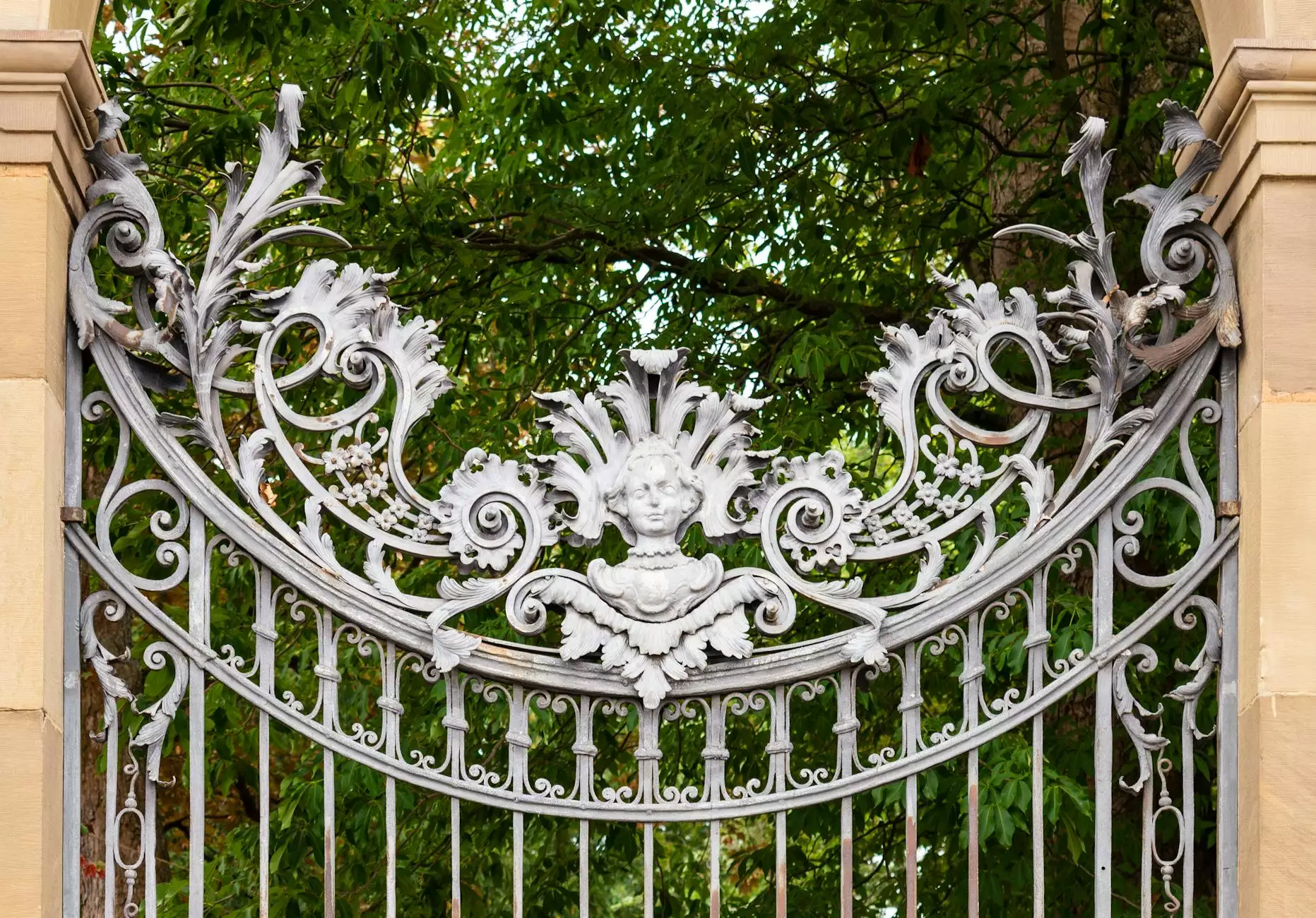
In the contemporary landscape of manufacturing, the significance of precision mould making manufacturers cannot be overstated. These specialized manufacturers are at the forefront of creating intricate moulds that are essential for producing high-quality products used in various sectors, particularly in electronics and medical supplies. The precision with which these moulds are crafted directly influences the performance, reliability, and efficiency of the final products.
What is Precision Mould Making?
Precision mould making is a sophisticated process involving the design and production of moulds that are used for shaping materials, often metals and plastics, into specific configurations. These moulds are synonymous with quality and precision, ensuring that every unit produced meets stringent standards and specifications. The importance of precision cannot be emphasized enough, particularly in industries that demand high reliability and safety, such as healthcare and technology.
The Importance of Precision in Mould Making
The phrase "precision is the mother of quality" rings particularly true in the manufacturing sector. Here are several key reasons why precision is paramount in mould making:
- Consistency: Precision moulds guarantee uniformity in product output, ensuring each item produced aligns with the desired specifications.
- Quality Assurance: High-precision moulds contribute to lower defect rates, leading to greater customer satisfaction.
- Cost Efficiency: Investing in precision moulds can drastically reduce production costs over time due to decreased waste and lower rework rates.
- Innovation Enablement: Precise mould making supports advanced designs and innovations in products, pushing the boundaries of what is possible in both electronics and medical devices.
Applications of Precision Mould Making in Electronics
The electronics industry is one of the most dynamic sectors that rely heavily on precision mould making manufacturers. From mobile phones to computer components, the role of precision moulds is vital for several reasons:
Complex Geometries and Designs
With the rapid evolution of technology, electronic devices have become increasingly complex. Modern electronics manufacturers require moulds that can produce parts with intricate designs. Precision mould making manufacturers leverage advanced technologies, such as computer-aided design (CAD) and computer-aided manufacturing (CAM), to create moulds that can accommodate these sophisticated designs reliably.
Material Versatility
The electronics industry utilizes a wide variety of materials, including thermoplastics, thermosetting plastics, and metals. Precision moulds made with innovative techniques help manufacturers adapt to diverse material requirements while maintaining strict tolerance levels. This flexibility allows for the prototyping of new products and the piping of mainstream models.
High-Volume Production
The demand for electronic products often leads to high-volume production runs. Precision moulds are designed to withstand extensive usage, delivering consistent results over time. This longevity is vital for manufacturers aiming to scale their operations without compromising on quality.
The Medical Sector and the Need for Precision Moulds
In the realm of medical supplies, the stakes are even higher. Products must not only meet legal and regulatory standards, but they also must function flawlessly in critical situations. Here's how precision mould making manufacturers serve the medical industry:
Compliance with Stringent Standards
Medical devices and supplies are regulated through stringent quality standards such as ISO and FDA regulations. This means that any deviation in the manufacturing process can lead to severe consequences. Precision moulds allow for a detailed manufacturing process that helps ensure compliance with these regulations, facilitating streamlined approval processes for new products.
Safety and Reliability
Products used in the medical field—such as syringes, IV bags, and prosthetic devices—must be manufactured with the highest levels of precision to ensure patient safety. Moulds that are made to exacting standards reduce the chances of errors, contributing to the overall effectiveness and reliability of medical supplies.
Patient-Centric Innovations
The evolution of medical devices often parallels breakthroughs in technology. With precision mould making, manufacturers can produce components that enhance patient care, such as ergonomic designs for comfort and usability. This innovation-driven approach is essential in improving patient outcomes and healthcare services.
Technological Advancements in Mould Making
The field of mould making has evolved significantly over the past decade, primarily due to technological advancements. These innovations have not only improved the quality of moulds but have also optimized the efficiency of the manufacturing process.
3D Printing in Mould Making
One of the most exciting developments in the industry is the integration of 3D printing technology in mould making. This technology allows for rapid prototyping and the production of complex mould designs that were previously impossible to create using traditional methods. Consequently, manufacturers can bring products to market faster, staying ahead of industry trends.
Automation and Smart Manufacturing
The rise of Industry 4.0 has paved the way for greater automation in mould making processes. By utilizing robotics and AI-driven solutions, manufacturers can significantly improve operational efficiency, maintain quality control, and reduce lead times. Operation while minimizing human error makes a compelling case for the benefits of automation in the mould making industry.
Quality Management in Precision Mould Making
Ensuring quality in mould making is not just about intricate designs; it is a comprehensive process that encompasses every aspect of production. Here are several key components of quality management within the industry:
Regular Calibration and Maintenance
Precision moulds must undergo regular calibration to ensure they remain within specified tolerances. This involves meticulous checks and adjustments to the machinery used in mould making. Preventive maintenance protocols help identify potential issues before they disrupt production.
Internal and External Audits
Implementing a robust auditing process—both internal and external—ensures that manufacturers adhere to industry standards and regulations. These audits facilitate continuous improvement and help identify areas where efficiency can be enhanced or costs reduced.
The Future of Precision Mould Making Manufacturers
Looking ahead, the future of precision mould making manufacturers appears promising. With ongoing advancements in technology, a growing emphasis on sustainability, and the ever-increasing demand for high-quality products across diverse industries, manufacturers are poised to expand their capabilities. Here are some future trends to consider:
- Increased Focus on Sustainability: As the green movement gains momentum, manufacturers will find ways to reduce waste and utilize biodegradable materials in mould production.
- Integration of AI and Data Analytics: By leveraging AI, manufacturers can analyze data for better decision-making, facilitating predictive maintenance and optimizing supply chains.
- Enhanced Collaboration: The future may see closer collaborations between mould manufacturers and end-users, resulting in tailored solutions that meet specific industry needs.
Conclusion
In conclusion, precision mould making manufacturers represent a cornerstone of modern manufacturing industries, particularly in electronics and medical supplies. Their commitment to quality, innovation, and precision shapes the products that improve lives daily. With advancements in technology and a keen focus on meeting industry challenges, these manufacturers will continue to lead the way toward a brighter, more efficient future in manufacturing.