Making Carbon Fiber Body Panels: Transforming the Automotive Industry
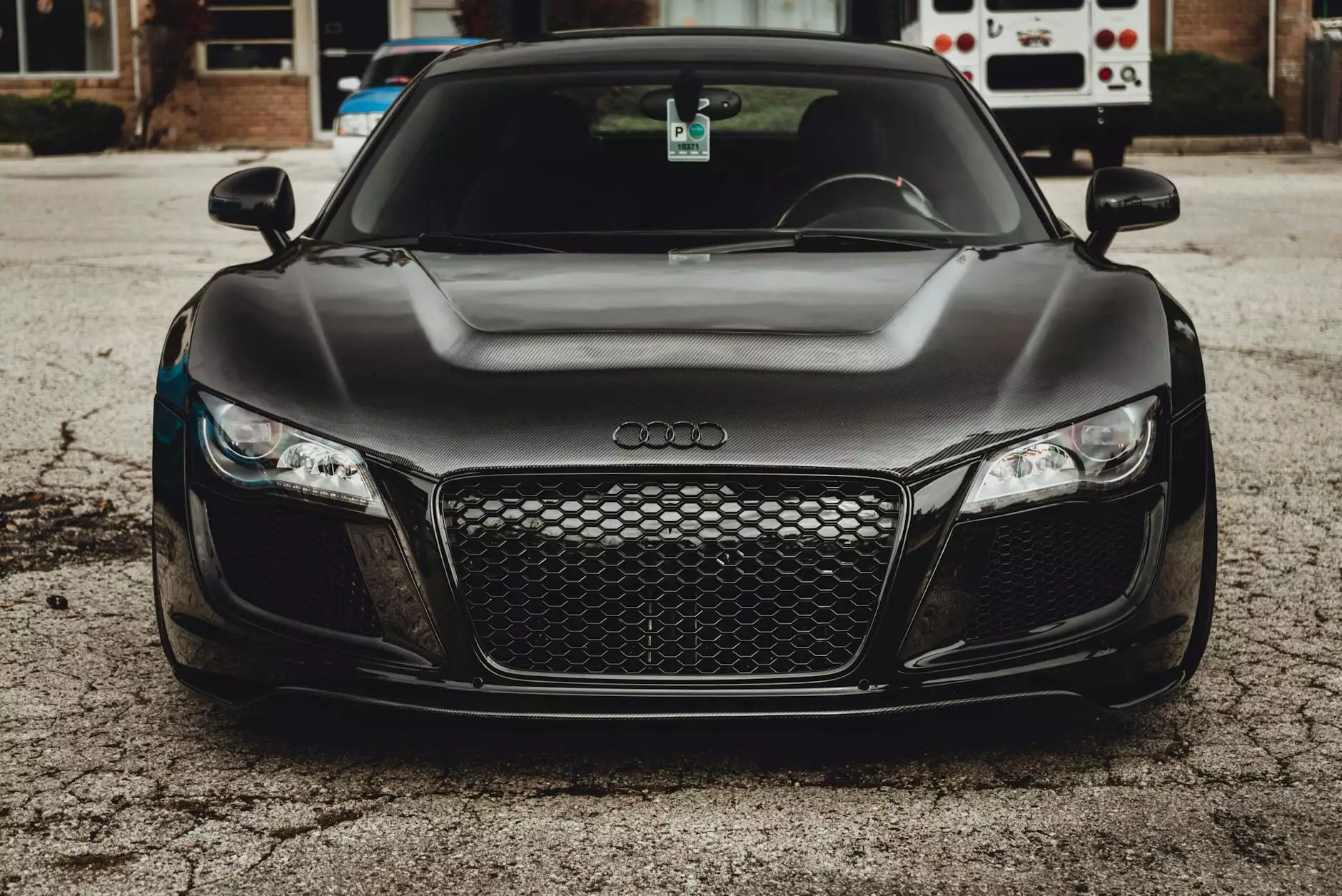
The automotive industry is continuously evolving, with innovative technologies paving the way for lightweight and high-performance vehicles. One of the most groundbreaking advancements in recent years is the use of carbon fiber body panels. This article delves into the art and science of making carbon fiber body panels, exploring their benefits, the manufacturing process, and the future of this incredible material in the automotive sector.
What is Carbon Fiber?
Carbon fiber is a lightweight, high-strength material composed of thin strands of carbon atoms. These strands are woven together into a fabric and then mixed with a resin to create a solid composite material. The unique properties of carbon fiber make it an ideal choice for various applications, particularly in industries where weight reduction and strength are crucial.
Why Use Carbon Fiber Body Panels?
- Weight Reduction: Carbon fiber is much lighter than traditional materials such as steel and aluminum, allowing manufacturers to reduce the overall weight of the vehicle.
- Increased Strength: Despite its lightness, carbon fiber is incredibly strong and stiff, providing excellent protection in the event of a collision.
- Enhanced Performance: Lighter vehicles can achieve better acceleration, braking, and handling, leading to an overall improved driving experience.
- Aesthetic Appeal: Carbon fiber has a distinctive look that many automotive enthusiasts find attractive, making it a popular choice for luxury and performance vehicles.
The Process of Making Carbon Fiber Body Panels
The process of making carbon fiber body panels involves several steps, each requiring precision and expertise. Here is a detailed overview of the manufacturing steps:
1. Design and Engineering
The first step in creating carbon fiber body panels is the design phase. Engineers use advanced software to create detailed 3D models of the panels, ensuring the specifications meet the performance and aesthetic requirements. This step includes:
- Designing the shape and dimensions of the body panels.
- Conducting simulations to test structural integrity and performance under various conditions.
2. Material Selection
Choosing the right type of carbon fiber and resin is crucial for achieving the desired properties. Manufacturers typically consider the following:
- Carbon Fiber Type: There are various grades of carbon fiber, each offering different strength and stiffness characteristics.
- Resin System: The resin used in conjunction with carbon fiber affects curing time, strength, durability, and resistance to environmental factors.
3. Preparing the Molds
Once the design is complete, the next step is preparing molds for the carbon fiber body panels. Molds are usually made from materials like aluminum or fiberglass. The process includes:
- Creating a prototype or master model to serve as a reference for the mold.
- Applying a release agent to the molds to ensure the finished panels can be easily removed.
4. Layup Process
The layup process is where the actual composite material is created. This step involves:
- Cutting carbon fiber sheets to size based on the specifications from the design phase.
- Layering the cut sheets in the mold, typically using a specific orientation to maximize strength.
- Applying the resin to the layers of carbon fiber, often through techniques such as vacuum infusion or hand layup.
5. Curing
Curing is a critical phase in making carbon fiber body panels, where heat is applied to solidify the resin. This can be performed in various ways:
- Oven Curing: Panels are placed in an oven to ensure uniform heating and proper hardening of the resin.
- Autoclave Curing: For high-performance applications, panels are cured under pressure, enhancing the material’s properties.
6. Trimming and Finishing
After the panels have cured, they need to be trimmed and finished. This step involves:
- Removing excess material and trimming the edges for a precise fit.
- Applying surface finishes or coatings to enhance the aesthetic appeal and protect the panels from environmental damage.
Applications of Carbon Fiber Body Panels
Carbon fiber body panels are extensively used in various automotive applications, reflecting their versatility and performance benefits. Some popular uses include:
- Sports Cars: Performance-oriented vehicles utilize carbon fiber to enhance speed and handling.
- Luxury Vehicles: Many high-end manufacturers incorporate carbon fiber for its aesthetic appeal and weight-saving properties.
- Racing Cars: The racing industry relies heavily on carbon fiber to maximize performance while minimizing weight.
The Future of Carbon Fiber in the Automotive Industry
The future of making carbon fiber body panels looks promising. As technology advances, we can expect to see:
- Cost Reductions: As manufacturing processes become more efficient, the cost of carbon fiber could decrease, making it accessible to more automakers.
- Increased Adoption: More automotive manufacturers will likely adopt carbon fiber as production techniques improve and demand for lightweight vehicles grows.
- Innovative Designs: The flexibility of carbon fiber will enable engineers to create even more complex and efficient designs in the future.
Conclusion
In summary, the process of making carbon fiber body panels is a sophisticated blend of art and technology, offering unparalleled benefits in terms of weight reduction, strength, and aesthetic appeal. As the automotive industry continues to evolve, embracing innovative materials like carbon fiber will play a critical role. By investing in this technology, manufacturers can produce high-performance vehicles that meet the demands of modern consumers.
For those in the automotive sector looking for superior auto parts and supplies or seeking partnerships with forward-thinking car dealers and brokers, customclass.net is your premier destination. Explore the endless possibilities that carbon fiber body panels bring to the automotive landscape and stay ahead in this competitive industry.